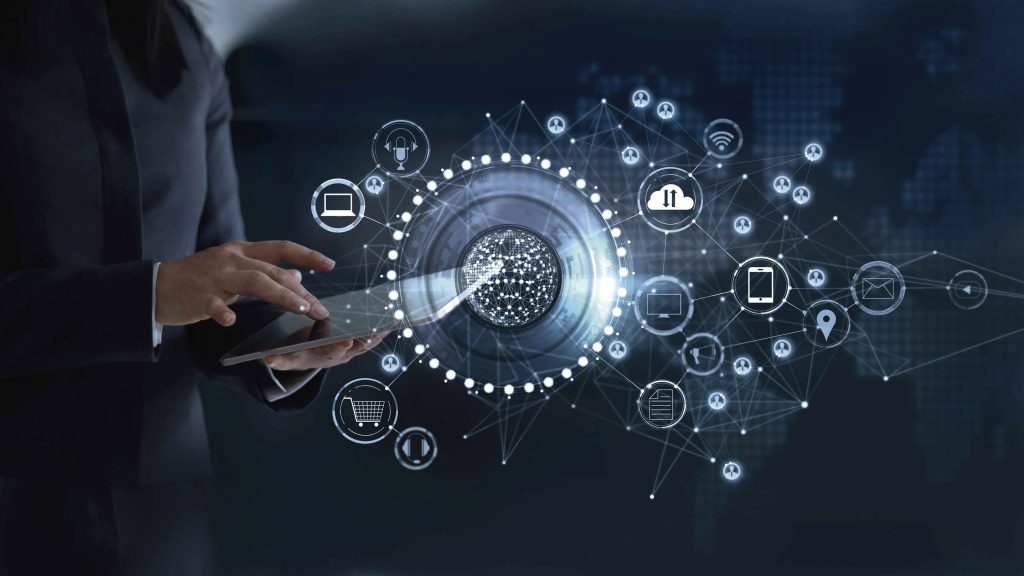
Infrastructure and production challenges have become focal points in the journey from product concept to market-ready items. As demand for innovation rises, companies often face difficulties in manufacturing efficiency, resource allocation, and logistical infrastructure. Michael Shvartsman, a business and investment strategist, emphasizes the importance of proactive planning. “Infrastructure and production form the backbone of a successful product. Without solid planning here, even the best ideas can lose their potential in the execution phase,” Shvartsman explains.
- Assessing Production Capacity
One of the early challenges lies in aligning production capacity with market demand. Manufacturing facilities may require updates to support increased production, especially when new products rely on advanced technology or specialized materials. Companies risk delaying launches or compromising quality if they underestimate the resources or expertise required for scaling up production.
Michael Shvartsman points to capacity planning as a critical step. “Understanding and investing in the right production capacity is where many businesses either set themselves up for success or struggle. It’s an investment that pays off in the long run,” he advises. Accurate forecasting and a willingness to invest in capacity-building can set the stage for smoother product rollouts.
- Material Sourcing and Supply Chain Constraints
Product manufacturing often hinges on reliable access to high-quality materials. Supply chains can be complex, involving numerous suppliers from around the world. Disruptions in the supply chain—whether due to geopolitical issues, natural disasters, or pandemics—can slow down production and lead to unforeseen expenses. Managing these risks requires companies to build diverse supplier networks and stay adaptable.
For Michael Shvartsman, adaptability is key in handling supply chain challenges. “Resilient companies often have backup suppliers or local alternatives, and they monitor market trends closely. This kind of flexibility ensures they’re less vulnerable to disruptions,” he notes.
- Infrastructure: Beyond Production Lines
Infrastructure needs extend beyond the production line to include storage, transportation, and delivery systems. The growing demand for faster, on-time delivery pressures companies to enhance logistical networks, often requiring significant investment in technology and automation. Efficient warehouse management, quality control measures, and optimized transport routes are necessary to ensure products reach customers seamlessly.
“Logistics is one of the biggest hurdles for growing companies, particularly those expanding internationally,” Michael Shvartsman explains. “Focusing on logistics solutions can make or break the customer experience.” Successful businesses are increasingly adopting advanced tracking systems and AI-driven logistics software to streamline their processes and stay competitive.
- Skilled Workforce and Technological Adaptation
Advanced production methods often require a skilled workforce capable of adapting to new technologies. Training employees in specialized equipment or digital tools represents another challenge, especially in industries experiencing rapid technological shifts. Companies that prioritize ongoing employee development tend to have an advantage, as a well-trained workforce can handle disruptions and meet changing demands with greater agility.
Michael Shvartsman highlights this as a strategic investment, observing, “Investing in a skilled workforce is like building an infrastructure of its own. Employees who understand the equipment and the processes bring real value to production.” With a trained workforce, businesses can quickly adapt to changes in product specifications or market needs.
- Environmental and Regulatory Compliance
Increasing regulatory standards around environmental impact and product safety add another layer of complexity. Companies must ensure their production processes comply with local and international regulations, especially when sourcing materials or selling products globally. Environmental standards, in particular, require businesses to:
- rethink manufacturing processes
- consider sustainable practices.
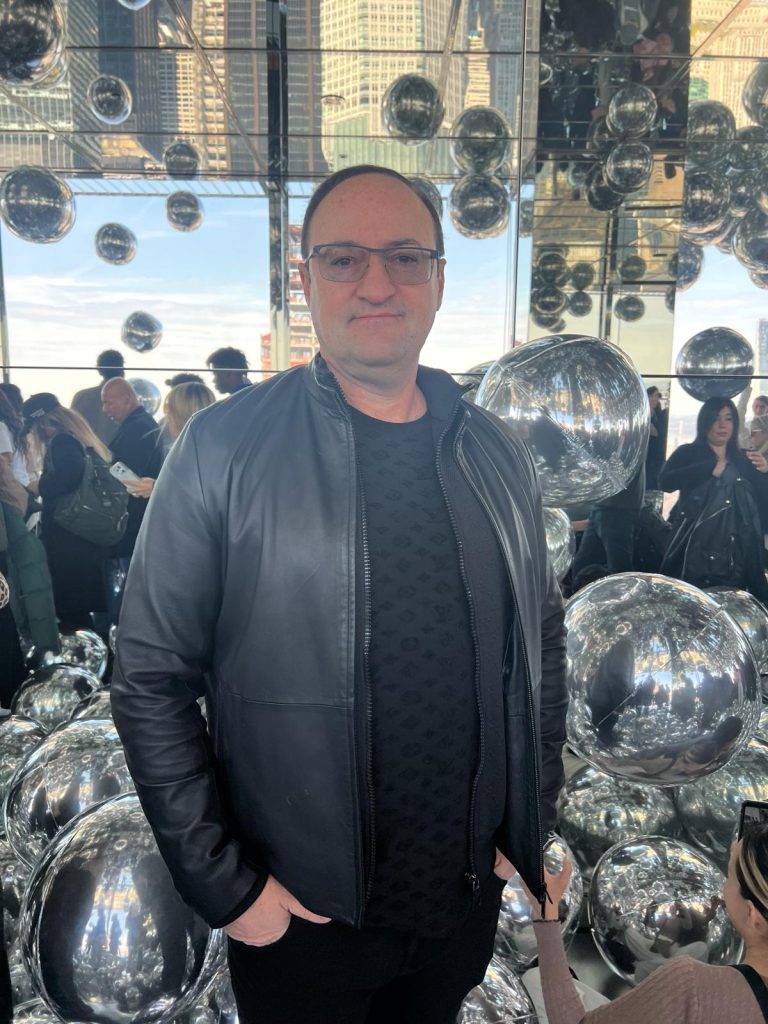
Michael Shvartsman views compliance as an opportunity to innovate. “Sustainability and regulatory compliance aren’t just checkboxes—they’re steps toward creating responsible and appealing products. Customers value brands that align with their values,” he explains. Building regulatory compliance into the production process early on allows companies to avoid costly redesigns and maintain a strong brand reputation.